El punto de partida para todo mapa de la cadena de valor es seleccionar la familia de productos dentro de su compañía, cada familia de producto es una cadena de valor y lo que se diagrama es cada cadena de valor. Diagramar o dibujar todas las cadenas de valor en un solo diagrama resultará muy complicado. Una familia de productos es un grupo de productos que pasan a través de procesos y maquinas o equipos similares, Ojo, esto es vital, no se confunda, una maquina puede procesar productos de varias familias de productos.
Los gurús Lean recomiendan que la empresas tengan un gerente de la cadena de valor, y por su puesto tienen razón, en Colombia varias empresas están creando el Gerente de la Cadena de abastecimiento, quien tendría como misión la integración de toda la cadena de abastecimiento, desde despachos hasta compras y almacén pasando por producción.
Dentro de las funciones de este nuevo Gerente esta en realizar Kaizen constante sobre el flujo de valor, mucho cuidado!!! No delegue la implementación del plan a futuro sobre los otros gerentes y cada quien implemente lo que le toca, es un grave error, es fracaso seguro, alguien debe ser responsable del todo y ese es el Gerente de la cadena de abastecimiento.
Hay dos clases de Kaizen, el Kaizen de flujo y el Kaizen de proceso. El Kaizen de flujo es que el que se enfoca en el mejoramiento del flujo de información y material, este está más que todo en manos de la gerencia y el mejoramiento de proceso es aquel que se enfoca en el mejoramiento del trabajo de la gente y en el mejoramiento de procesos, este lo ejecuta más que todo el personal de planta.
El mapa de la cadena de valor tiene 4 elementos:
1. Seleccionar la familia de productos.
2. Dibujar el estado actual.
3. Dibujar el futuro deseado.
4. Plan de acción e implementación.
El dibujar el futuro deseado es el más importante de todos los elementos, ese es el objetivo, un mapa del estado actual sin el futuro deseado no sirva para nada.
Algunos consejos para Mapeo:
· Siempre recolecta la información que usaras en el dibujo del estado actual por ti mismo y en planta, camina por la planta, recolecta la información de primera mano, de la gente, no de mediciones anteriores o viejas.
· Siempre empieza por el proceso más cercano al cliente, puede ser en muchos casos el área de despachos, une vez recolectes la información allí inicia el recorrido hacia arriba hasta llegar al inicio del proceso, la materia prima.
· Lleva tu cronometro, toma tiempos por ti mismo, no confíes en viejos informes de tiempos, la información veraz es clave.
· Haga el mapa por usted mismo, pero no solo, el mapa se debe hacer con la gente de la planta, al inicio con sus supervisores y luego exponerlo al personal para que realicen sugerencias.
· Siempre dibuje a lápiz o sobre un tablero, no use computador, ni software, lo perfecto es enemigo de lo práctico.
Pasos para dibujar el estado actual.
1. Siempre empezar dibujando el ícono del cliente y colocar en la caja de datos la información pertinente a este.
2. Dibujar los procesos empezando de izquierda hacia la derecha, es decir por la materia prima hasta el cliente.
3. Llena la caja de datos de cada proceso.
4. Dibuja los inventarios entre los procesos con el ícono del triangulo y coloca la información correspondiente.
5. Dibuja los proveedores, en la caja de datos coloca su capacidad, y dibuja el camión que representa las entregas de este.
6. Dibuja las flechas correspondientes al flujo Push, al flujo de información y el de suministro, desde la derecha hacia la izquierda, es decir, comenzando por el cliente hacia el proveedor pasando por programación.
7. Dibuja la línea de tiempo en donde colocas el tiempo que no agrega valor y el tiempo que agrega valor.
No se preocupe, estos pasos sin mayor información pueden ser confusos, seguido de esta entrada iniciare a explicarlos con un ejemplo para la claridad de todos.
A continuación les copio algunos de los íconos y su significado:
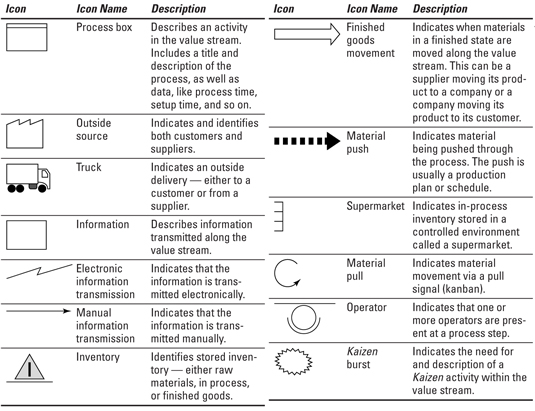
